基本的には当サイトでは、週末の時間をつかって暮らしを豊かにするために役立つものを出来るだけ簡単に短時間に加工することをテーマとしています。
いっぽうで、若干ハードルが高くなったとしても、いろんなことに挑戦したみたいという気持ちもあります。そんな相容れない中で、結局は自分の気持ちに素直になり行動するようにしています。
ホゾ接ぎを選んだ時点で、作業時間は長くなることは想像できますが、その中で出来るだけ簡単に作業できるように工夫することに注力してみました。
相欠き接ぎ(ホゾ接ぎ)をつかってお風呂の目隠しをつくろう
CADを使って面格子のレイアウトを検討
モノを作るとき、まずはイメージが大事になってきます。作業をシュミレーションしながらほんとうに実行可能な内容かを確認していきます。その後の実際の加工作業の中で、改善点が出ることはありますが、まずは叩き台を作ることにより前進できる。
とにかく、始める。
CAD上では、原寸大で自由に発想できます。まずは、お風呂の窓枠を採寸してスケッチするところから始まります。
風呂場の面格子レイアウト案
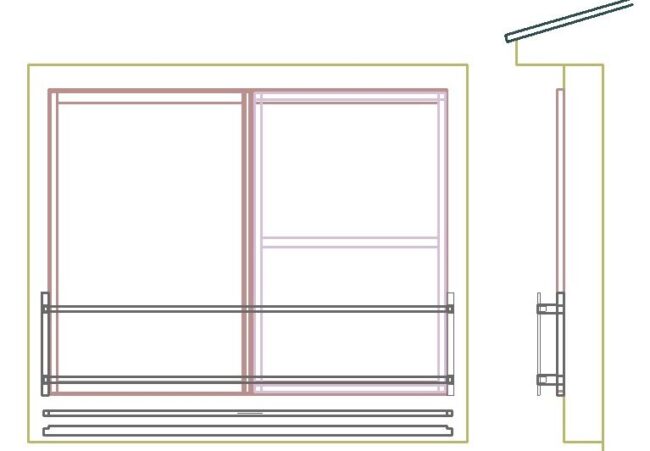
ビス止めとホゾ接ぎの選択
実はどちらの方法でも製作できますので、好みで選べば良いとおもいます。そのどちらを選択するかによる違いをまとめると次のようになります。
ビス止めとホゾ接ぎの比較 | ||
項目 | ビス止め | 相欠き接ぎ |
作業時間 | 短い | 長い |
作業難易度 | 比較的かんたん | 比較的むずかしい |
仕上がり寸法 | 厚くなる | 薄く仕上がる |
変形しやすさ | ビス1本では変形 | 変形しずらい |
美観(サビ) | ステンレスビス、キャップなど | スッキリ |
現在は時間的にゆとりがあるため、ホゾ接ぎを選択していますが、もしも、急ぎの場合はビス止めを選択すると思います。
外観(美観)の違い ビス止めとホゾ接ぎ
ビス止めにするか、ほぞ接ぎにするかによって、下図のように仕上がり外観に若干の違いが出てきます。
ビス止めでは、材料同士をクロス又は平行に重ねて施工します。一方、ホゾ接ぎでは木材同士を組み合わせるため、木材の張り出しが少なくスッキリとした外観に仕上がります。また、雨水がかかる場所で使用する場合は、腐食を防ぐためにステンレス製のビスを使いましょう。
ビス止めとホゾ接ぎのレイアウト比較
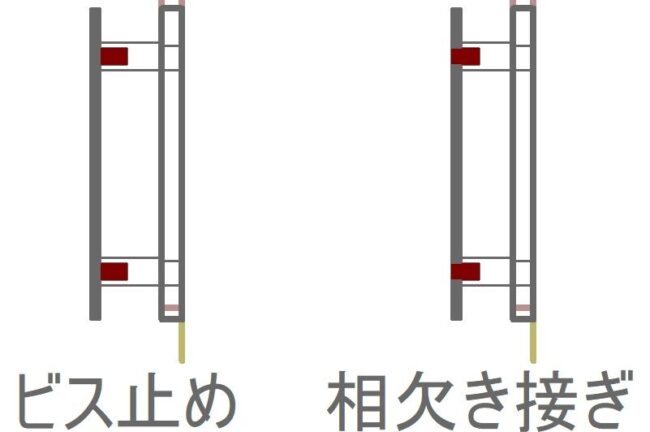
ビス1本止めでは回転方向に変形しやすい。
今回の格子面のように細い材料をビス止めするとき、おのずと使用するビスの本数に制限がでてくる場合があり、細い材料をクロスさせて固定する場合ではビスを2本止めるのが難しくなります。こういうケースでは、下イラストのように1本のビスを回転中心として材料が回転するように動いてしまいます。
ビス止めのデメリット ビス1本止めでは不安定
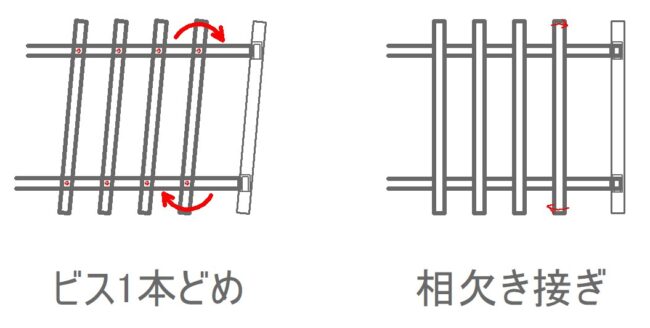
格子の支持方法と窓枠への設置方法を検討
施工方法が決まるまでは、アイデアを出しては問題に直面することを繰り返すことで何とか製作可能な考えをまとめることができました。
固定方法 その1 ALC壁にビスで固定
格子の支持方法の原案は下イラストのように、基礎になる角材にホゾ接ぎで短い柱(緑線)を組んでから、格子の横フレームをホゾで組み込む予定でした。
しかし、この方法では格子部分が窓枠よりかなりはみ出す構造となってしまいます。これでは家の前に駐車した車の横を通行する際に邪魔になるため、この案は見送りとしました。
面格子を壁に固定する方法 【ALC壁にビス止め】

固定方法 その2 アルミ角パイプでサッシ枠を挟む
格子のはみ出し問題を解決するために格子の支持方法も変更しています。柱を無くして格子の横フレームを基礎角材(2分割構造)に挟み込み、さらにサッシ枠のツバ部分を挟み固定する構造としています。
サッシ枠を挟み込む際の裏当てとして、アルミの角パイプ(端材)を利用して、ボルトで2分割構造の基礎角材をまとめて締め付ける構造としています。
しかし、この方法ではボルトがギリギリであることと、ナットが表側にきて美観が今一つであるため見送りました。
面格子を壁に固定する方法 【アルミ角パイプで挟む】
-e1674422298614.jpg)
固定方法 その3 アルミフラットバーをサッシ枠に固定して挟む
こちらは最終案となります。ボルトは見栄えが良い六角穴付きボルト(キャップ)を使い基礎角材に深座ぐりを加工してボルトのはみ出しを抑えます。
裏当てにはアルミフラットバーを使用して、アルミフラットバーと基礎角材でサッシ枠のツバを挟み込んで、まとめてボルトで締め付けます。念のため、アルミフラットバーはサッシ枠のツバにビス止めしています。
面格子を壁に固定する方法 【アルミフラットバーで挟む】
2-e1674422325315.jpg)
面格子DIY 相欠き接ぎの加工のために準備したもの
我が家は北向きの玄関であり、玄関には柔らかい光が差し込み特に暗い印象はありません。そして、お風呂がある北向きの窓側は直射日光が避けられるため網戸などの建材の痛みが少なくて済むようです。
前回つくった木製の回覧板受けももちろん玄関脇に設置していますので、北向きの恩恵を得て変形や痛みがなく良好な状態を維持できています。
ということで、同じく北向きに面した浴室の目隠しとして、木製の面格子を設置してみようと思います。もしも、陽当たりのよい南向きや、西日が強い場所では木の変形が考えられるため、あまりおススメしませんが、北向きの場所や、比較的陽が差し込まないような条件でしたら木製の面格子は目隠しとして効果的だと思います。
もしも、強い日差しが当たる場所に面格子を設置するのであれば、私ならアルミ製の目隠しを考えると思います。
材料の準備
窓枠は1間(約1800mm)あり、途中に支柱を入れることができませんので、反りが少なくキレイなエゾ松を使用します。
エゾ松 幅60mm×厚さ24mm×長さ1820mm 3本
エゾ松 幅24mm×厚さ14mm×長さ910mm 15本
アルミフラットバー 幅30mm×厚さ3mm×1000mm 1本
エゾ松の角材とアルミフラットバー
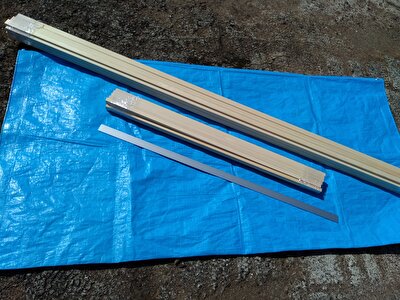
使用した工具
・ノコ(7寸目、ゼットソー)
・トリマー(ほぞの加工)
トリマーでホゾを加工
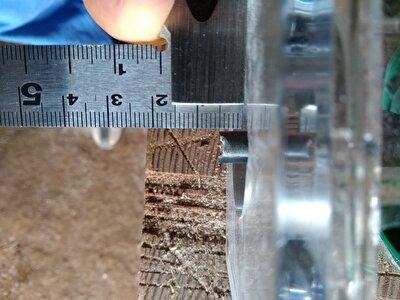
・ノミ(ほぞの仕上げ)
・充電ドリルドライバー
・ドリル
アルミフラットバーにドリルで穴をあける
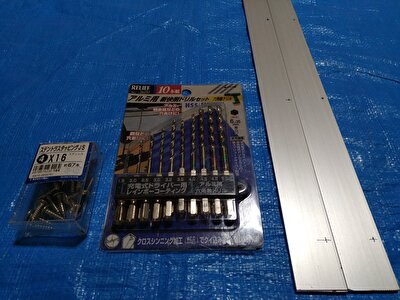
・六角レンチ
・モンキーレンチ
・ゆるみ止め
ステンレスのボルトで固定(ネジのゆるみ止め剤)
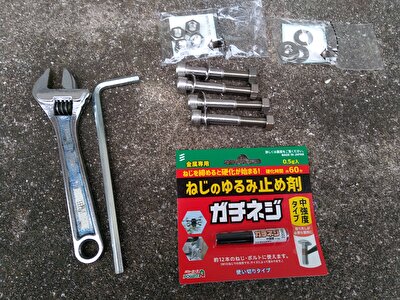
面格子DIY 相欠き接ぎの加工手順
格子はホゾ接ぎをおこなっていますが、相欠き接ぎは比較的に簡単なタイプのホゾ接ぎであるため初心者にもおすすめです。しかし、このホゾ接ぎは、構造上はめ込んだだけではしっかり固定できるものではありません。(特に相欠き部分が浅い場合)
そこで、わたしはボンドでホゾ接ぎ部を接着して、面格子を接ぎ終えたあとの形をしっかりと保持させています。
作業手順 1 格子の作成
面格子の制作に使用した木材はいずれもエゾ松で、横フレームは十分な強度を持たせるために厚みを24mm、たわみを少なくするために高さを60mmとかなり大きくしています。縦に組み込む格子は厚み14mm 幅24mmとし、横フレームの厚み24mmにたいして、縦に組み込む格子は厚み14mmと異なる厚みとしています。
縦に組む格子は数が多いので、出来るだけ軽くするために14mmと薄い材料を選んでいます。そのため、格子の切り欠きは3mmとかなり浅くしています。(相欠き部を深くすると破損しやすくなるため)
格子の加工寸法

① 材料の切断 ― 無駄を出さないサイズ ―
格子の大きさはエゾ松の販売サイズに合わせて決めています。使用した木材は幅24mm×高さ14mm×長さ910mmのもの。これをちょうど真ん中で切断して2本の格子を取れるサイズとしています。
販売サイズの材料を半分にカット
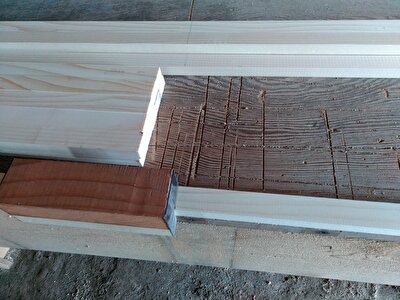
② 相欠き部をノコで切り込み ― ケガキ線で繊維を断ち切る ―
この工程でホゾの切り欠き部の幅が決まりますので、ほぞ接ぎの大事な部分となります。木材の販売では、サイズを表示していても実際のサイズは若干違うことが良くあります。ですから、接ぎ合わせる木材のサイズを一度確認してからケガキ線を入れると後の調整作業を少なく抑えることができます。
トリマーをかける準備 ノコで切り込み
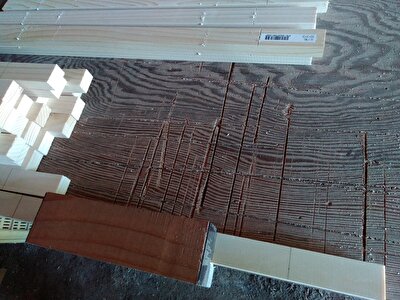
③ トリマー作業の準備 ― 材料の即席ガイド ―
電動工具を使用する際は、材料をしっかり固定することが大事になります。万力やクランプで固定すると安心なのですが、今回の格子のように数量があるときはセッティングを繰り返すだけで作業の負担が増えてきます。
そこで、作業を安全に、出来るだけ楽にできるように工夫すると良いでしょう。私は近くにあった端材(角材2本、板の切れ端)をL型クランプで固定することでゲート状の固定治具としています。
即席のトリマーガイド

④ ケガキの2~3mm内側をトリマーで加工 ― 際がキレイ ―
木材への切り欠きを加工する際、ノコで切り込みを何本か入れることノミで簡単に切り出せることを紹介していますが、それとほぼ同じことをしていると言えます。
作業のポイント
木材は繊維が束ねられたような構造となっているので、部分的に繊維を切断するとこと、その部分は繊維の束から浮いた状態となっています。そのためノミやトリマーの衝撃で比較的簡単に線維の束から外れてくれるのです。
トリマーで切り込みの際を除去
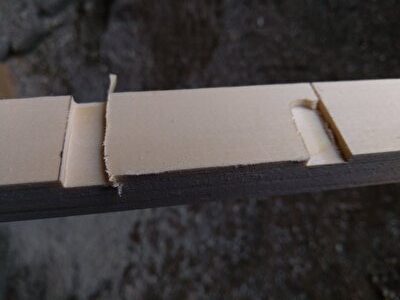
トリマーベースを接地させ安定させる
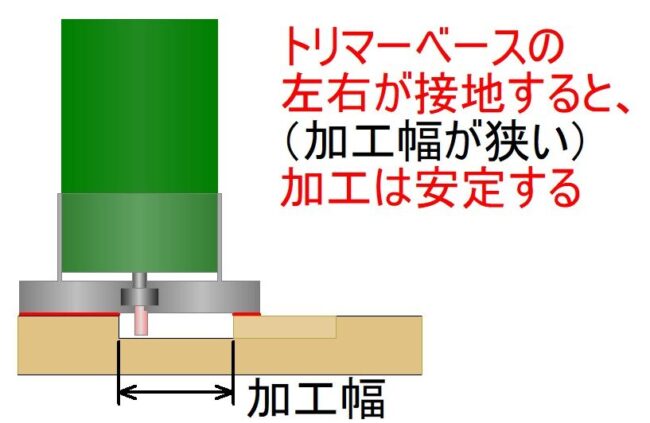
⑤ 中央部をトリマーで削る ― 最後は鑿で仕上げ ―
トリマーを使用する際は、トリマーベース(ベースプロテクタ)の大きさと加工する部分の大きさを考えてから加工手順を決めることが大切です。
トリマーによる加工を安定させるには、トリマーベースを幅広く当てるのが理想です。今回の格子のように細長い部材では、出来るだけトリマーベースの左右が設置している状態が理想となります。
ほぞ接ぎでは、組み際の仕上がりが見た目を大きく左右するため、私は上の写真のように相欠き部の際を最初に加工して後から中央部を加工しています。しかし、下の写真のように切り欠き部の底面に波が出ているのが分かると思います。これは加工プランを考えずに作業したため材料に対してトリマーベースの接地状態が悪くなってしまったことが原因だと考えられます。
つまり、トリマーベースの幅と切り欠き部の幅を考慮して、トリマーベースの接地を長く保てるように加工プランを考えることで、加工面の仕上がりがきれいになると思われます。
また、トリマーベースの左右が接地する状態を保てない場合、無理して片側のみの接地で加工するより、ノミを併用することも検討すべきだと思います。
トリマーでホゾ部を除去
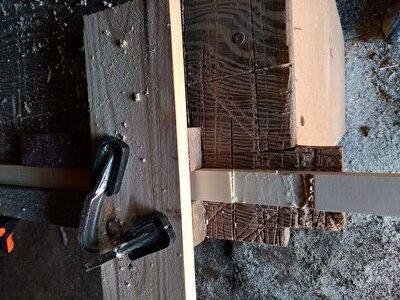
例1 トリマーを安定させる接地のしかた
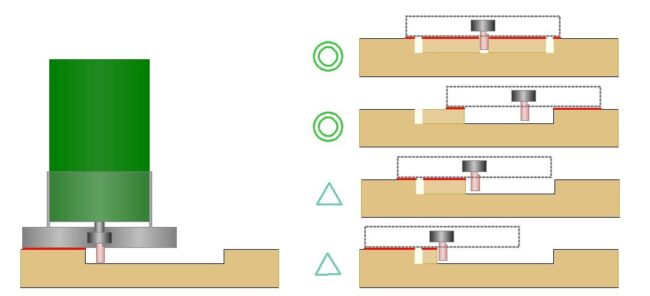
例2 トリマーを安定させる接地のしかた
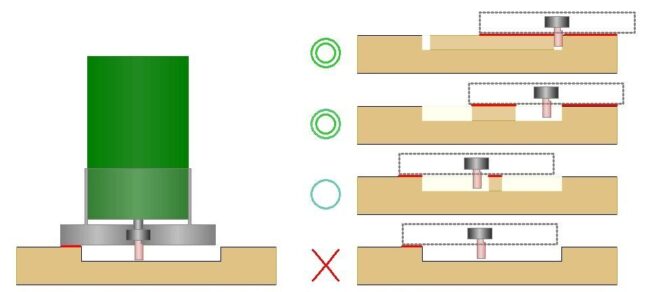
トリマーを使った溝加工について
・上図から分かるように、トリマーベースの左右が材料に接地している場合は安定して加工を行えます。
・溝の加工幅が広くなった時(トリマーベースと同じくらい)、中央から加工して左右に逃げるのか【例1】、あるいは中央をある程度残すことでトリマーベースを左右接地させることで安定を保つ【例2】。
・【例1】はトリマーベースの片側を広く接地できるものの、片側のみの接地となりやや不安定。【例2】は最後に残った中央部をトリマーで取ってしまうのは危ない。
・下図のようにトリマーを安定した姿勢で加工できる範囲を取り除き、残りの細い部分にノミを(ウラスキを上にして)あて軽くたたくと、ポロポロといった感じで除去できます。
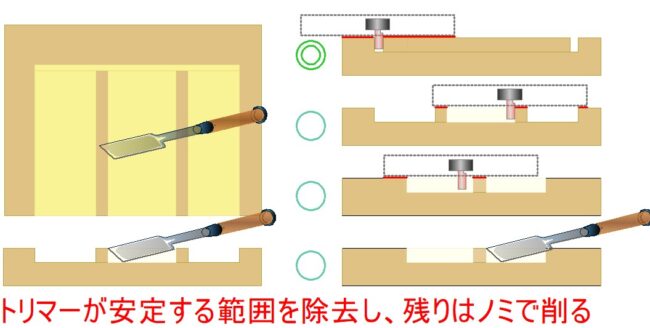
※状況にあわせて、加工方法を使い分けるのが良いと思います。
⑥ 格子の相欠き部のミゾ幅の確認 ― すべての格子が噛み合う ―
横フレームの板幅60mmに対して、格子に加工した相欠き部の溝幅が不足していないかを確認。キツ過ぎる場合はノミ又はノコで調整して、すべての格子を隣り合わせながらはめ込み出来る状態であることを確認しています。
格子を仮にかみ合わせ
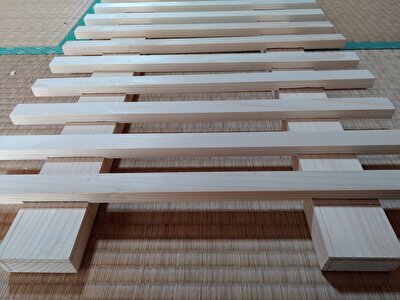
作業手順 2 格子の横フレーム作成
元々は40mm×24mmの角材を横フレームに使用することを考えていました。しかも、横方向に40mm、縦方向に24mmとしていました。この時は北風に対する横方向の強度を優先するような考えでした。
しかし、基礎角材に支柱を立てない構造に変更したことから、横フレームの端部が強固に支持されるため、風による横方向へのたわみは少なくなると考えています。
むしろ、数多く取り付ける格子の重さと、横フレームの重さによるたわみ(下方向への曲がり)が心配になったため、高さ60mm×幅24mm×長さ1818mmとしています。(はりの高さ方向を大きくするとたわみは少なくなります。)
格子と横フレームの取付け

① 横フレームへ相欠き接ぎのケガキ ― 格子が垂直になるように ―
横フレームは上段と下段に1本づつあり、格子がそれぞれに直角に交わる構造となります。もしも、上下にあるの横フレームに加工する相欠き接ぎの溝の位置がズレてしまうと格子が斜めになってしまいます。
そのため、上下のフレームを下の写真のようにL型クランプでしっかり固定した状態でケガキを行っています。このようにしておけば、格子のピッチは多少狂うことがあっても、上下のフレームでほぞ接ぎの溝の位置がズレることはありません。
上下の横フレームを同時にケガキ
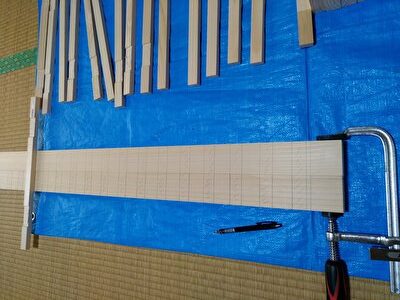
② 相欠き部をノコで切り込み ― ケガキ線で繊維を断ち切る ―
ケガキ線に沿って木の繊維を断ち切るための切り込みを7寸目ノコを使って入れています。その際、木材に対してノコギリを直角に当てるために、ほぞの胴付き部を加工するための治具を使っています。
ノコで切り込み 繊維を断ち切る
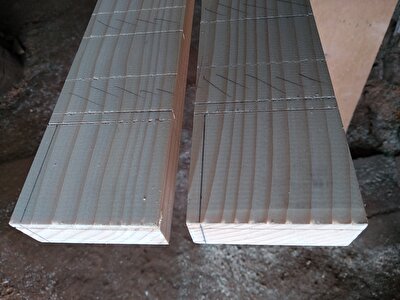
③ ケガキの2~3mm内側をトリマーで加工 ― 片側をまとめて ―
加工のコツとして、連続的な作業ではシンプルな工程にしぼり、同じ作業を繰り返した方が効率が良いものです。(時として、飽きることもありますが。)
下の写真では、横フレームの溝加工で向かって左側のみを連続して加工しています。通常右利きのかたならトリマービット位置と左側のラインとの位置関係が把握しやすく、トリマーのコントロールがしやすいのではないかと思います。
ですから、下の写真の状態で29カ所の溝の左のみを加工して、その後横フレームを180°反転させます。
トリマーでケガキの際を取り除く

④ ケガキの2~3mm内側をトリマーで加工 ― 反対側と中央 ―
同じように向かって左側を29カ所の溝の左のみを加工しています。その後、中央に残った部分を除去します。トリマーを使えば、こういった狭い溝なら比較的に加工しやすいのではないかと思います。
トリマーでほぞの噛み合い部を除去

⑤ 相欠き部の仕上げ ― 鑿でなめらかに ―
これくらい狭くて浅い溝であれば、トリマーの姿勢が安定して加工しやすい条件が整っているので、加工面の仕上がりはかなりキレイになると思います。
それでも、どうしても多少の段付きが発生してしまうものです。そんな時は、ノミを使って軽く削ることで、段をとり除いたり、あるいは溝の際の部分に残った木の繊維を削りホゾの入隅をきれいに仕上げると、相欠き接ぎを組みやすくなります。
ノミを使って溝を仕上げ

⑥ 変則的な二方胴付き平ほぞ接ぎ ― 二方と三方の中間タイプ ―
プロが行う高度なほぞ接ぎでは、接着剤など使用せずそれだけでしっかりと固定できるものがあります。
私と同じのように、ウィークエンドにDIYを楽しむ者にとっては、あまりにもハードルが高すぎるのでその領域を目指してはいませんが、簡単なほぞ接ぎを一度経験してみると、手間がかかるものの、得られるメリットの大きさに気づくのではないかと思います。
ほぞの構成を分解して考えると、穴加工(ほぞ穴)と凸部加工(ほぞ)に分けられます。そして、手加工の場合、(角穴ドリルを使うと簡単にできる)難易度が高いのはノミによる穴加工ではないかと思います。
例えば、最もシンプルな二方胴付き平ほぞ接ぎを例に考えると、ほぞを接いだときに胴付き(段に加工している部分)のところは、ホゾ穴が見えなくなります。一方、胴付きが無い面ではホゾ穴にホゾが入り込んでいる様子がそのまま見えるのです。そのため、穴の仕上がりが具合がそのまま見えてしまいます。
つまり、手加工ではキレイに加工するのが難しいホゾ穴の加工キズをほぞの胴付き部で隠すことができるメリットがあります。
面格子の接地場所と通常の目線を考えると、見られるのは正面と上面となるため、胴付きを正面と上面にしています。(通常の二方胴付き平ほぞ接ぎでは、正面と裏面に胴付きを加工します。)
もちろん、凸部になるホゾの胴付き部のカットの仕上がりが見た目を左右することになるのですが、私の経験上、治具を使うことで初心者でもかなりキレイに仕上げることができます。
変則的な二方胴付き平ほぞ接ぎ
-e1674422609984.jpg)
変則的な二方胴付き平ほぞを加工
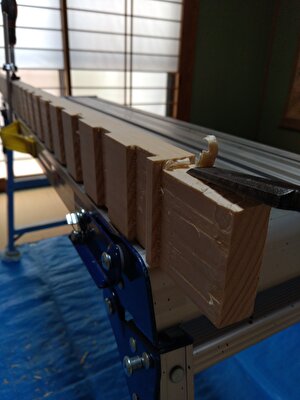
一般的な二方胴付き平ほぞ接ぎ

三方胴付き平ほぞ接ぎ

作業手順 3 基礎角材の加工
今回のDIYにおいて、製作前の検討段階で一番苦労した部分となります。
・丈夫であること
・張り出しが少ないこと
・格子部のたわみが少ないこと
・固定したときの見た目がキレイなこと
図面による検討では、面格子の固定方法や、組み方、フレームのサイズなど随分と変化していきました。
結果として、構造はいたってシンプル。フレームのサイズも一回り大きめ(冬場の北風を意識して)にしたので、どちらかというとオーバースペックぎみかもしれません。前回の引違い戸で採用した二枚の木材を合わせた構造により、面格子の支持部強度の確保とホゾ穴の加工をしやすくしています。
基礎角材の加工寸法

① 2本の角材を合わせてケガキ ― 基礎角材のホゾ穴 ―
2本の角材をクランプで固定した状態で、ホゾ穴のケガキをおこなっています。
基礎角材のほぞ穴をケガく
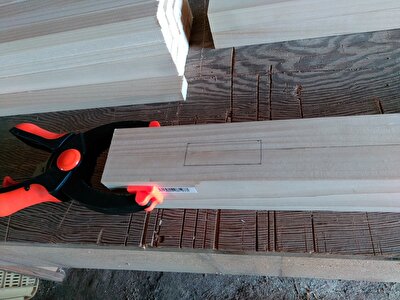
② ホゾ穴を加工 ― 2分割することで加工の難易度を下げる ―
7mm深さ(右側用1本、左側用1本)、12mm深さ(右側用1本、左側用1本)
トリマーで削る前に、ノミでケガキ線のやや内側に切り込みを入れて木の繊維を切る。
2分割してほぞ穴加工

③ トリマーによる加工
トリマーの加工では、私と同じ右利きのかたはケガキ線の右側を倣いながら加工した方がやり易いのではないかと思います。
1)ケガキ線の内側を縁取るように削る
下の写真からも分かるように、左側を縦方向に加工する時はトリマービットとケガキ線を認識しやすいため加工ラインが比較的に安定しているのに対し、奥の方を横方向に加工する際はケガキ線を認識しずらいために加工ラインが安定していません。
ケガキ線からはみ出さないようにトリマーで削る

2)トリマーにより半分除去
左の方から、少しづつ削っていきます。この時、トリマーベースは広い範囲でしっかりと木材に当たるため、加工を安定しておこなえます。
左半分を除去

3)右端を残して除去
下の写真から分かるようにトリマーベースが左右と上の3方向において、常に接地する条件ではトリマーの姿勢が安定するため加工後の面はほとんど荒れていません。
トリマーベースが広く接地する範囲で除去

4)材料の向きを反転して、ケガキ線の右側を削る
前項3)の状態から、残った部分をそのまま加工しても構いません。ただその場合、ブラインド加工(トリマービットでケガキ線が良く見えない)状態となってしまうため繊細な加工が難しくなってきます。
下の写真のように、いったん木材を180度反転させることでトリマービットとケガキ線の両方を認識できる状態となりますので、加工が楽になります。
材料を反転して、トリマービットとケガキ線が見えやすい状態で加工

③ サッシ窓枠の形に合わせて削る ― 鉋で仕上げ―
基礎角材と3mm厚のアルミフラットバーにより、お風呂のサッシ枠を挟み込む構造としているのですが、基礎角材の裏面がフラットなままでボルトを締めあげると基礎角材は斜めに傾いてしまいます。
そのため、サッシ枠の厚み分を逃がすための浅い(3mm)溝を加工しています。ただし、この逃がしのための溝が深すぎると、ボルトを締めてもサッシ枠を挟み込む十分な力を発生することができなくなりますので注意が必要です。
加工のポイント
実際のサッシ枠の厚みよりやや浅めに加工するのが良いと思います。木材は金属と違い、ある程度の凹凸や突起部を当たり面で吸収する柔軟性があるため。
それから、下の写真は実際に削った時のものです。このような段差を加工する場合、トリマベースの接地面は片方だけになってしまうため(本来なら、最初に同じ厚みの板をガイドとして準備してから加工をするのが望ましい。)トリマーの姿勢が安定しません。
このような状況において削り残した部分を削る場合、もしも同じ板厚の材料がある場合は隣に置いてトリマーベースを預けられる状況をつくるのが良いでしょう。あるいは、カンナで削って仕上げるのも一つの方法です。
基礎角材の裏面にサッシ枠の「逃がし」を加工
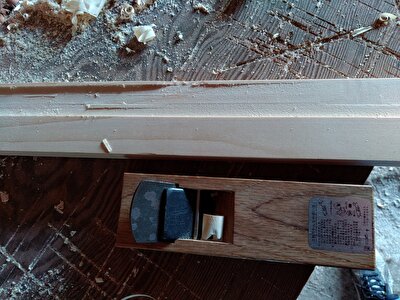
④ ホゾ穴の確認 ― 2分割の木材にホゾ穴 ―
二分割の木材にホゾ穴を加工する場合は、ホゾ穴の深さと穴位置のズレがないように細心の注意が必要となります。穴位置のズレは、そのまま2つの木材の外部の合わせ部に段差となって影響しますので、穴の加工にズレがないように修正が必要です。
また、ホゾ接ぎのはめ合いにつていは、ホゾ(凸部)で調整するほうがやり易いでしょう。
ホゾのはめ合いを調整
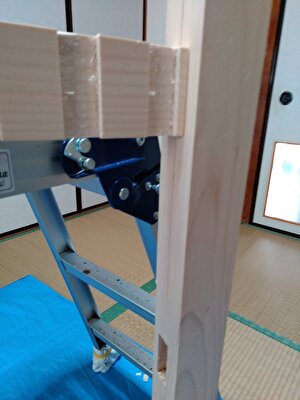
「胴付きほぞ」にしているため、上の写真のようにホゾ穴加工の切り口(加工キズ)が見えなくなります。
⑤ ホゾ穴の確認 ― 格子のピッチと基礎角材のホゾ穴の一致 ―
今回の面格子のように密接してほぞを接ぎ合わせる場合、一つ一つは合っていても隣とのズレある場合に上手く組付けできなくなることがあります。
あるいは、単純に単品の加工寸法が悪いために組付けできない場合があります。(数量が多い場合は、どうしても加工精度の個体差が生じやすくなります。)
基礎角材のほぞ穴と格子の穴ピッチを確認
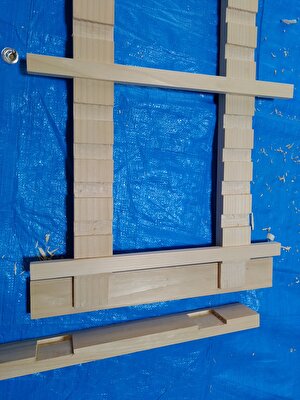
作業のポイント
ボンドを使った本組付けを行った後に塗装をすると、もしも接着剤(透明)がはみ出し場合に接着剤自体は透明であるために目立たないとしても、接着剤の上に塗料はきれいにのらないために仕上がりが汚くなってしまいます。
ですから、ほぞ接ぎ部を接着する場合は、後から調整が発生しないように塗装工程に入る前に必ず仮組みしておきましょう。
基礎角材、横フレーム、格子を仮組して確認
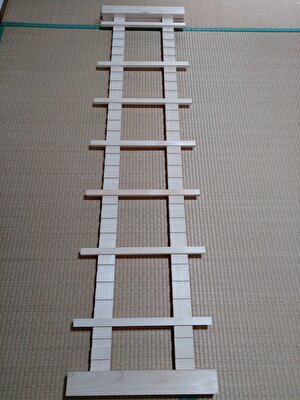
※上の写真では格子を間引いていますが、すべての格子を仮組して確認しています。
作業手順 4 塗装作業
塗料は防虫防腐水性塗料を使用しています。前回制作した回覧板受けで使用した黒色が余っていたことと、家の外観の統一感を考えて今回も黒色を選択しています。
本来なら、素材である木の質感を活かすために茶系の塗料が良いのかもしれません。そうすれば2~3回の重ね塗りで綺麗に仕上がります。
しかし、黒色を選択する時点で塗装作業が大変になることは覚悟しなくてはいけません。(仕上がりに求める黒色の濃さにもよりますが)
① 作業準備 ― マスカーで床を養生 ―
使用する材料も塗料も回覧板受けとほぼ同じであるため、今回も7~8層の重ね塗りを覚悟して取り掛かっています。(裏面は3層塗りをイメージしていますが、実際の色を見て判断します。)
塗装作業は長期戦と考え、焦らずじっくりと作業を組立てています。
面格子本体よりも十分広い範囲を養生
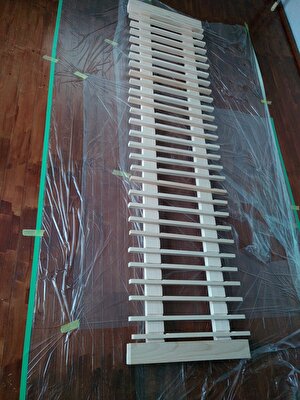
② 1層目の塗装 ― 上面と側面 ―
塗装では焦りは禁物です。欲を出して次々と塗っていくと塗料が垂れてきて仕上がり汚くなってしまいます。
重ね塗りといっても、塗った塗料が乾かないうちに次の塗料を塗っても色は出ません。
また、縦の面の塗装では油断するとすぐに塗料が垂れてきますので十分注意しましょう。
格子をばらして、基礎角材、横フレーム、格子を塗装
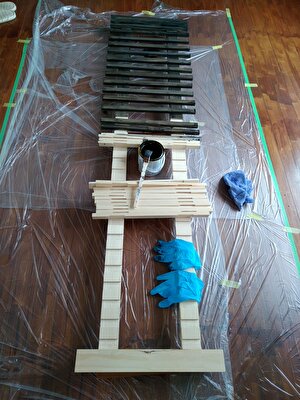
表面1層目の塗装を完了
エゾ松は木材の中でもかなりの色白です。そのため、正直なところ黒色の塗料との相性はあまり良いとは思いません。
黒色の塗料とはいえ、1回塗っただけでは下の写真のようにかなり薄い感じとなります。
表面一層目の塗装完了
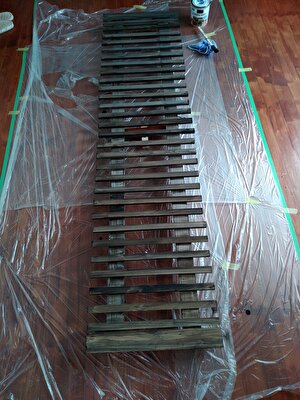
② 裏面の塗装 ― 1層目の塗装完了 ―
格子は横フレームから外して、下の写真のように井形に組んだものを一つ取っては隣に井形を組み上げる形で塗料を塗っています。
裏面1層目の塗装

裏面 3層重ね塗り
格子の井形の位置が横にズレているのが分かるかと思います。とにかく焦らず、塗料が乾いてから、2層目の塗料を塗り、2層目の塗料が乾いてから3層目の塗料を塗ります。
下の写真のように、遠目に見る分には、それなりに色が出てきましたので裏面の塗装は3層の重ね塗りで終了します。(裏面は人目に触れることはありませんので、このくらいで十分だと判断しています。)
裏面は3層重ね塗り
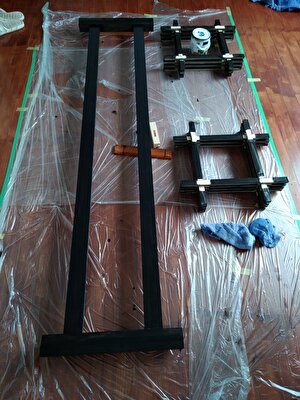
③ 表面の重ね塗り ― 格子の側面は裏返しながら ―
とにかく焦らずに、粘り強く重ね塗ります。格子の正面を上にして左右の側面を塗ることも出来るのですが塗料のタレやすいので、可能なら塗りたい面を上面に水平の状態にすると塗装作業をやり易くなるので理想といえます。(側面を塗装すると塗料がたれて塗装面が汚くなる)
格子の側面を塗装
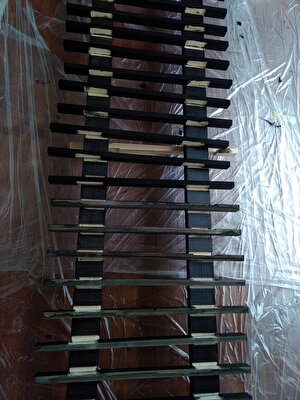
④ 全体の仕上げ ― 裏面3層重ね塗り 表面7~8層重ね塗り ―
漆黒の黒。 ここまでくるとサッシのカラーアルミに見劣りしないので、一体感がでます。
表面は7~8層重ね塗り
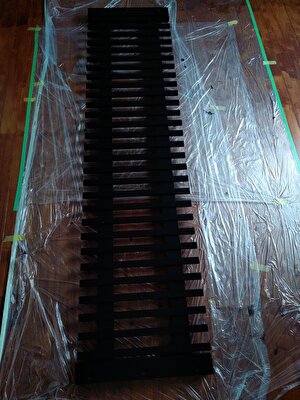
面格子DIY 現場への設置作業
CADは実寸で図面を引けるのが大きな特徴といえます。今回のように既存のサッシ窓枠に何か取付けをおこなうような場合、いろんなアイデアを検討してみて実現可能(製作、取付けできるか?)かを検証できます。
しかし、CAD上では分かっているとは言っても、この取付け穴位置は出来を映えを大きく左右するため、いちど実寸を測って確認するのが良いでしょう。
窓枠へのアルミフラットバーの取付け
下の写真はビスの下穴に対して、問題なくネジを締め込めるかを確認しているところです。本来このタイプのタッピンねじは薄鋼板に適しているようです。
やや厚めの鋼板(4~5mm以下)では2種や3種のタッピンねじが適しているようです。あるいは、セルフタッピングねじなど
私が使用したビス
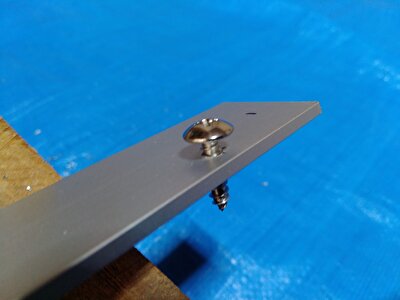
・4mmのタッピンねじ(余っていたものを使用)
・下穴3.2mm(板厚3mmのアルミ材)
タッピングねじ それとも タッピンねじ?
どちらが正しいのでしょうか? JIS B 1122 によると ” タッピンねじ “ と表記されています。しかし、私も今回調べるまでは気づいてなかったのですが、慣例的に” タッピングねじ ” ” タッピングビス ” のいずれでも通用するかと思います。
【JIS B 1122 十字穴付きタッピンねじ】によりねじ部は1種~4種に分けられています。
詳しくは ネジの百科事典 タッピンねじ をご覧ください。ちなみに上の写真のような今回使用したタッピンねじは最も一般的な1種です。主に薄鋼板(1.2mm以下)、ハードボード、木材、石綿に使用します。
メートルネジと違いタッピンねじの下穴は板厚により変わってきます。詳しくは、タッピンねじの標準下穴径 をご覧ください。
タッピンねじ 1種(A型)標準下穴径表 | ||||||
板の厚さ | 呼び径 | |||||
3.0 | 3.5 | 4.0 | 4.5 | 5.0 | 6.0 | |
0.4 | 2.2 | 2.6 | 2.8 | |||
0.6 | 2.3 | 2.6 | 2.9 | 3.4 | 3.8 | 4.5 |
0.8 | 2.5 | 2.8 | 3.0 | 3.5 | 3.9 | 4.7 |
1.0 | 2.6 | 2.9 | 3.1 | 3.6 | 4.0 | 4.9 |
1.2 | 2.6 | 2.9 | 3.2 | 3.7 | 4.1 | 5.0 |
引用元:ネジクルHPより
※ちなみに、下穴が小さすぎるとネジは入らないし、下穴が大きすぎるとネジが緩すぎてしっかり締まりません。
下穴の選定(ボルトとナットを組み合わせる一般的なメートルネジでは)
一般的に使用される並目ねじでは、呼び径-ピッチ=下穴径 (ネジ山が100%の完全ネジ)と覚えると便利です。これはポリテクセンターのベテラン講師に教えて頂いた事ですが、現職においても大変役立っています。(実際の現場では状況に合わせて少し大きめの下穴にすることがあります。)
メートルネジ | ||
呼び径 | ピッチ[mm] | 下穴径[mm] |
M3 | 0.5 | 2.5 |
M4 | 0.7 | 3.3 |
M5 | 0.8 | 4.2 |
M6 | 1.0 | 5.0 |
M8 | 1.25 | 6.8 |
M10 | 1.5 | 8.5 |
アルミフラットバーに下穴を加工 ― 下穴3.2mm ―
あとで分かったことですが、今回使用したタッピンねじは薄鋼板に適しているようです。幸い使用した材料がアルミ材(比較的やわらかい金属)ということもあり、問題なく使用できたようです。
アルミフラットバーに下穴を加工
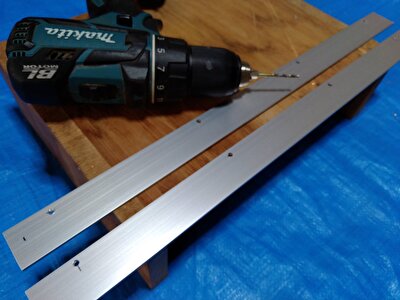
サッシ枠に現合にて2.5mmの穴あけ ― イラスト 解説① ~ ③ ―
アルミフラットバーには、タッピンねじの下穴をあけてあり、実際にはアルミフラットバーはサッシ枠の裏側に使用するため下穴の位置は確認できません。
そこで、下の写真のようにサッシ枠の手前がわにアルミフラットバーをクランプで固定し、穴加工位置を油性ペンで目印しても構いません。(アルミフラットバーを外してから穴加工)
あるいは、アルミフラットバーにあけたタッピンねじの3.2mm下穴よりも小さい径のドリルで直接穴をあけても構いません。(できれば下のイラスト解説のように、同じ径のドリルでもみつけして穴芯をだしてから、穴加工を行うのが理想)
サッシ枠に現合穴あけ加工
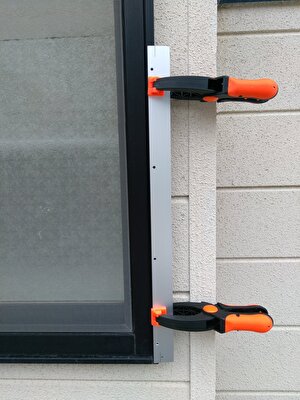
穴あけ工程のイラスト解説
・イラストの工程①・・・アルミフラットバーの下穴径3.2mmと同じ径のドリルで「もみつけ」る(くぼみをつける)ことで穴芯の目印となる。
・イラストの工程②・・・もみつけたくぼみに細いドリル(Φ2.5mm)を当てると、自然に穴の中心にドリルがセットできます。
・イラストの工程③・・・細いドリル(Φ2.5mm)で貫通
・イラストの工程④・・・太いドリル(Φ4.5mm)でタッピングネジ(4mm)を逃がすための穴加工。
・イラストの工程⑤・・・タッピングねじを締め付け、サッシ枠の裏側にあるアルミフラットバー(厚み3mm)が固定された状態。
※②~③の工程では、アルミフラットバー(グレーで表示)をつけたまま(上側イラストFBあり)でも、アルミフラットバーを外して(下側イラストFBなし)作業をおこなっても構いません。
アルミフラットバー下穴用のドリルで穴芯をもみつける(FBあり)

アルミフラットバー下穴用のドリルで穴芯をもみつける(FBなし)
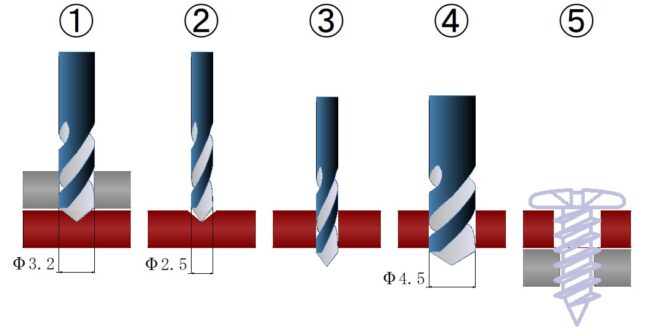
作業の反省点
今回の作業では、上の写真のようにクランプでアルミフラットバーを固定した状態で、イラスト解説の工程①を省略しています。そのため、若干の穴位置がズレてしまい、タッピンねじを斜めに締めることになりました。
まだ、イラスト解説の工程①のように「もみつけ」で止めないで、Φ3.2mmのドリルでそのまま貫通させるやり方のほうが良かったかもしれません。但し、イラスト解説の工程①でそのまま穴をあけると、ドリルのガイドとなる板(アルミフラットバー)の穴が若干削れて穴が大きくなることがあります。
サッシ枠にボルト穴を加工 ― イラスト解説 ④ ―
4mmのタッピンねじを使用して、サッシ枠の裏側に当てたアルミフラットバーをネジで引っ張る状態(しっかりと固定)にするたは、サッシ枠にネジ部が引っ掛からないようにタッピンねじより少し大きな穴をサッシ枠にあける必要があります。
そのため、ネジの頭(8.1mm)より小さく、ネジ部(4mm)より少し大きい4.5mmの穴をあけます。
現合での穴位置決めでは、アルミフラットバーにあけた3.2mmの下穴より大きなドリルを使用できないため、手間はかかりますが4.5mmのドリルに交換して穴を大きくします。そうすることは、しっかりとした締結力を得るには必要な工程となります。
サッシ枠にボルト穴を加工
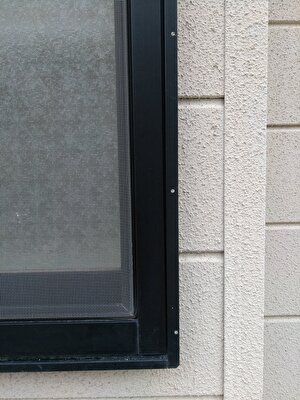
現物合わせ(現合)による穴加工
現物合わせの穴加工の方法としては、他にも先にサッシ枠に4.5ミリの穴をあけて、その後30mm幅のアルミフラットバーをサッシ枠の裏に当て、4.5ミリの穴から油性ペンで目印を書くという方法でも構いません。(イラスト解説 もみつけが適さないため、マーキングする事例)
下のイラスト解説の工程③では、裏側にくる材料をクランプなどでしっかりと固定出来て、なおかつ上側の板がある程度の厚みがないと「もみつけ」はできません。
工程③の「もみつけ」あるいは「マーキング」が終了したら、イラスト解説の工程④~⑤では裏側にくる材料を外して穴加工を行って構いません。
イラスト解説 「もみつけて穴芯をだす」

イラスト解説
「もみつけが適さない」ため、マーキングする事例(薄板の場合)
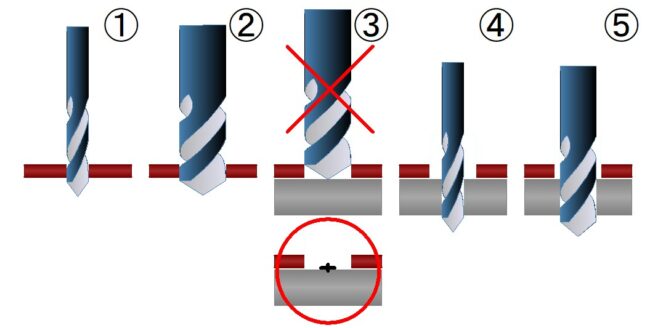
※上記イラスト解説のマーキングでは、「もみつけ」による穴芯の位置決めより精度は落ちてしまいます。
アルミフラットバーをサッシ枠に固定 ― ビス止め ―
本来の構造として、基礎角材とアルミフラットバーにてサッシ窓枠を挟み込むことで面格子本体を固定するようにしています。つまり、このビスの目的は、次工程のボルト穴をあける作業のためのもので、フラットバーの落下防止としています。
ですから、実はタッピンねじは2本くらいでも問題ありません。なぜなら、基礎角材はM8ボルト3本でしっかり締め上げますので十分な締結力がありまったく問題ないと考えているからです。しかし、折角ですからより安心感を高めるための処置としてタッピンねじを4本使用しています。
アルミフラットバーの固定
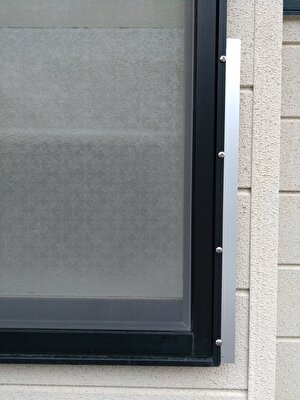
基礎角材の取付け
毎回のことですが、「思いを具体的な形にする」というのはなかなか大変な作業となります。いろんなアイデアを出しては、自分にダメ出しを繰り返し、やっと形になったのがこの基礎角材の取付け方法です。
いたってシンプルな構造なので、製作はそれほど難しくは無いと思います。
穴あけ ― 深座ぐりとボルト穴の加工 ―
今回使用したのは、見た目にちょっとオシャレな六角穴付きボルト。左右の基礎角材にそれぞれ3本づつM8のボルト ナットを使用しています。
深座ぐりで、ボルトを沈めると外観がよりスッキリします。但し、CADで書いたように六角穴付きボルトが完全に沈むほど深い座ぐりにはしていません。
深座ぐりを行うときは、材料の厚みをよく考え強度不足とならないように注意が必要です。特に、木材では金属と違いボルト締結であまりボルト締めすぎると木材はつぶれていきます。ですから、深座ぐりをあえて浅めにして残りの板厚を確保できるようにしています。
深座ぐりとボルト穴の加工
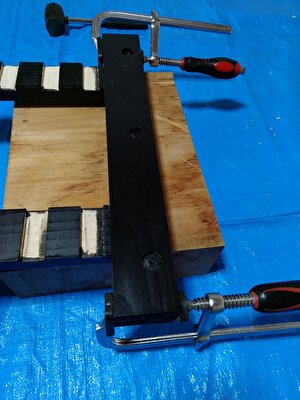
接着 ― 基礎角材をボンドで貼り合わせ ―
セメダイン スパーX にて基礎角材を貼り合わせています。接着剤はクリアタイプであるため、仮にはみ出しても目立つことはないのですが、接着してから塗装すると接着剤が邪魔して塗料が上手くのらなくなることがありますので、一番最後に接着作業をおこなっています。
基礎角材をボンドで固定
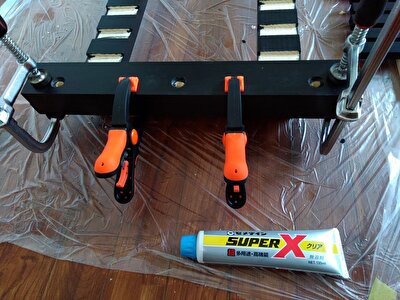
基礎角材の穴位置をマーキング ―ドリルで「もみつけ」―
私が作業した時間帯では、レーザーが見えない状況でしたので今回は水平器をあてて面格子の横フレームの傾きを確認しています。
あらかじめ基礎角材にあけていたボルト穴(下イラスト解説②)と同じところへ、アルミフラットバーにも穴をあけるため「もみつけ」(下イラスト解説③)を行います。
ドリルで現合もみつけとボルト穴加工

アルミフラットバーに現合によるボルト穴加工
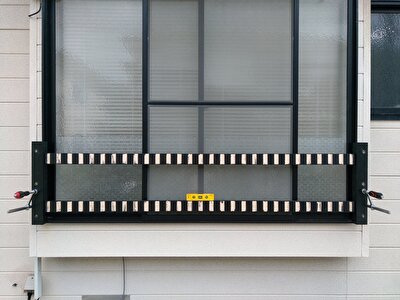
M8ボルト用として穴あけ ― ボルト穴9mm ―
上のイラスト解説④~⑤を行ったものが下の写真となります。上のイラスト解説④~⑤では基礎角材がある状態でアルミフラットバーに穴をあけるように表現していますが、イラスト解説③の「もみつけ」を行った後は面格子(基礎角材)を外してから④~⑤の穴あけを行っています。
アルミフラットバーにボルト穴を加工
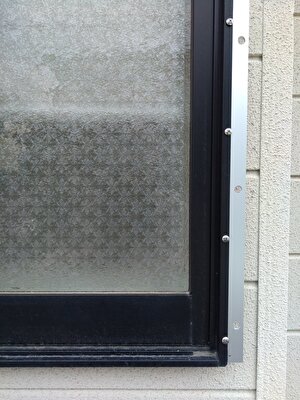
面格子の最終組み立て
前行程のアルミフラットバーに9mmのボルト穴をあけた後、いちど基礎角材とアルミフラットバーにボルトを通してみて、ボルトの取付けが出来るかを確かめてから最終組み立てに入ります。
面格子の組み立て
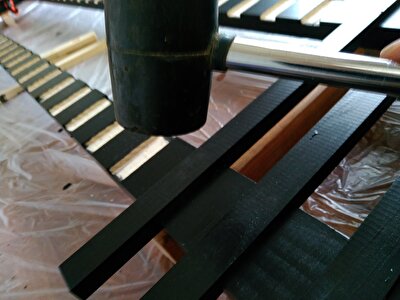
相欠き接ぎのはめ合い面に セメダイン スーパーX を塗ってから格子をはめ込みます。少しきつめのところはゴムハンマーで軽く叩いてはめ込んでいます。
ボルト止めによる面格子の固定
下のイラストのように、ボルトの頭が完全に隠れるように深座ぐりを深くはしていません。また、ボルトの穴位置と横フレームのホゾ部の位置をずらしているため下のイラストのようにホゾにボルトが貫通したような構造とはなっていません。
サッシ枠、アルミフラットバーと基礎角材をボルトで固定
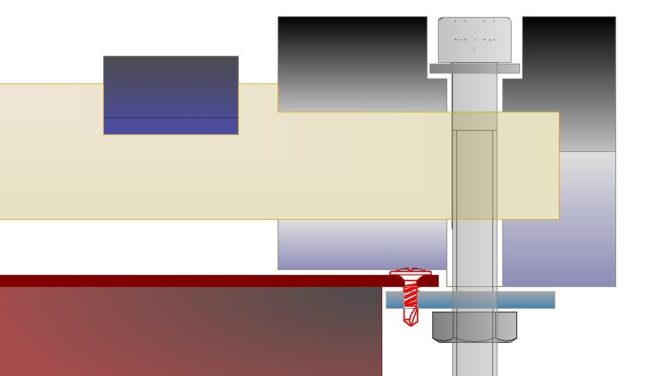
このイラストからも分かるように、接着した2枚の基礎角材は一体となり、さらにボルトで裏側のアルミフラットバーとでサッシ窓枠をしっかりと挟み込んでいます。
使用したボルト類と工具
ステンレス製 M8×60mm 六角穴付きボルト、平ワッシャ、ナット
六角レンチ、モンキーレンチ (13mm スパナ)、ゆるみ止め
面格子を固定するボルト、ナットとゆるみ止め
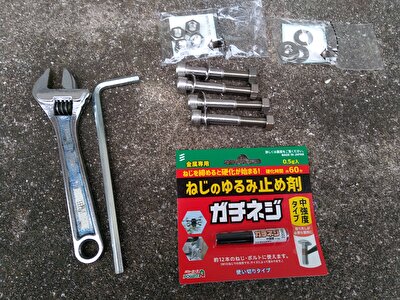
ネジにゆるみ止めを塗布
ガチねじ(ねじロックの類似品)は嫌気性固着剤です。つまり、空気に触れている間は固まることはなく、ボルト、ナットをしっかり締めてネジ部の空気が無くなると固まります。
・ねじ部のゴミ、汚れ、油分をよくとり除き乾燥させてください。
・ネジ部にガチねじを塗布してからナットを締め付けます。材質にもよりますが、1時間~2時間で実用強度に達します。
商品表示の使い方より
アルミフラットバーとボルト(赤いゆるみ止め)、ビス
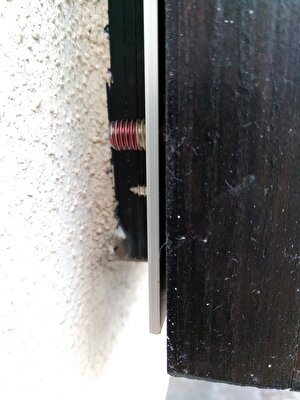
六角穴付きボルト(CAP)による固定
六角ボルトを使用しても特に問題ないのですが、深座ぐり加工をして六角ボルトを使用する場合、六角ボルトの頭が深座ぐりの中にもぐった状態のままで、工具を使って締め付けなければいけません。そうなると大きな径の深座ぐりが必要になってしまいます。
その点、六角穴付きボルトは六角レンチをボルトの正面から挿して使用するため、小さい径の深座ぐりで良いことから、深座ぐりとの相性が良くなっています。それから、風呂場の窓の前に駐車している車との間を通ることがあるため、面格子からの突起を出来るだけ避けたいという思いもあります。
あとは、個人的な好みとして六角ボルトよりも六角穴付きボルトのほうが見栄えが良い思っていることも選定した理由です。
ボルトは深座ぐりの中に沈み見た目スッキリ

ボルトによる固定 その裏側の様子
下の写真を見ると、タッピンねじが傾いているのが分かります。これはイラスト解説で示した施工のコツの工程②から始めたことが原因となっています。
本来であれば、工程①の「もみつけ」をおこなうことで、穴芯の狂いを防ぐことができタッピンねじをまっすぐに締め付けることができます。しかし、工程①を省いたために僅かに穴芯が狂ったことで、タッピンねじが傾いたのです。
基礎角材、アルミフラットバー、ボルトとナット、ビス
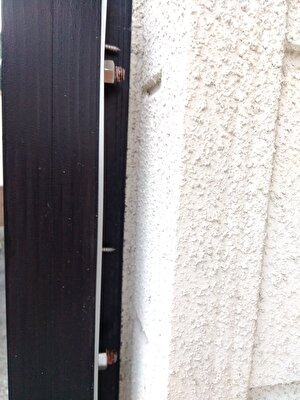
作業前と作業完了後の比較
作業前 風呂出窓の外観
浴室の出窓には樹脂製ブラインドを設置しているのですが、長さが不足していて以前から多少は気にはなっていました。
それでも一応、サッシ窓は板ガラスが使用されていて、さらにガラスの下部には目隠しシートが貼ってあります。
面格子を取り付ける前
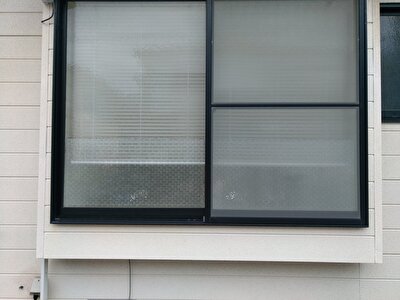
作業完了 風呂出窓に設置した面格子
ブラインドの長さが足りなかった窓の下部を面格子で囲うことができました。格子の間隔をあまりに狭くすると、浴室内が暗くなりすぎるので、少し広めにしています。
面格子を取付けた後
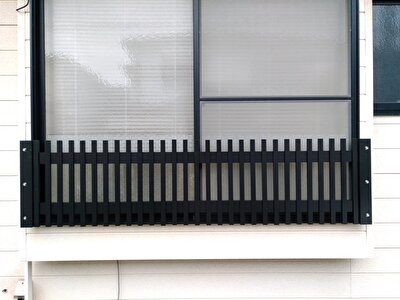
やはり、黒の塗料をじっくりと粘り強く塗って良かったと思います。窓枠との一体感がありほとんど違和感がないのではないかと自己満足の仕上がりです。
作業完了 風呂からみた出窓の様子
ブラインドの部分は必要に応じて開閉できますが、面格子は後から調整できないので参考にしていただけたら幸いです。
面格子のなかには、格子部をスライドさせて光の透過を調整できるようにした物もあるようです。我が家の場合、風呂が面している北側は冬場の北風が結構強いのでシンプルで丈夫な構造にしています。また、格子を少なくすることで風を受け流すことも期待しています。
風呂から透けて見える面格子
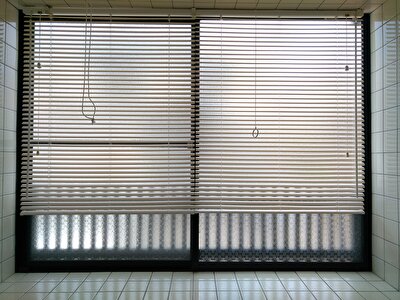
まとめ
風呂の窓については、少しは気にはなっていましたが、男の一人暮らしということもあり放置していました。
この作業に手を付けたきっかけは、余った黒い塗料でした。回覧板受けを作った時に買った塗料がまだだいぶ余っていてたことと、同じく北面に設置した木製の回覧板受けは変形することもなく良い状態を維持できていることから、木材で面格子を作っても大丈夫だろうと考えたから。
最初はもっと簡単に考えていたのですが、構造を具体的に決めるまでにかなりの時間が掛かってしまいました。あとは、最初から覚悟を決めて取り掛かっていた黒色の塗装ですが、やはり簡単にはいきません。とにかく手間がかかります。
もしも、エゾ松に黒色の水性塗料を塗ることをやってみようとお考えの方がいましたら、是非、根気強く、焦らず、じっくりと取り組んでみて下さい。
プロモーション |